下記の例はテクノベインズ社内にてDTPソフト CorelDrawを用いて出力したバーコード例です。
このテストでは、レーザープリンタにより出力したものです。
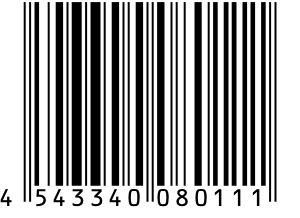 |
|
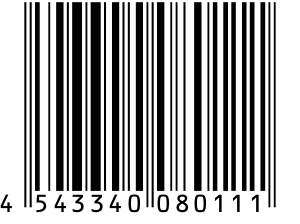 |
|
左は標準設定のまま生成したバーコード。 右はプリンタ解像度に調整して生成したバーコードです。肉眼での見た目はほとんど同じであると思います。
しかし実際にレーザープリンタで印刷したものを検証機をかけると、右の調整したものはA - 4.00と
最高品質を示すのに対して、標準設定のまま生成したシンボルはB - 3.00とグレードがかなり低くなります。
|
|
|
|
|
バーコード判定としてはどちらも合格が出ています。 |
概要:
シンボルグレード |
B - 3.00 / 06 / 660 |
スキャングレード |
B/3 |
|
|
概要:
シンボルグレード |
A - 4.00 / 06 / 660 |
スキャングレード |
A/4 |
|
|
しかし、グレード判定ではかなりの差があることがわかります。 |
寸法グレード:
デコーダビリティ |
57% |
B |
平均バー幅の増加 |
-0.002X |
OK |
|
|
寸法グレード:
デコーダビリティ |
64% |
A |
平均バー幅の増加 |
+0.007X |
OK |
|
|
検証の詳細数値結果では、左のバーコードではデコーダビリティ 57% B が原因でグレードを下げていることを示しています。
デコーダビリティの値により、以下のようにグレードが決定します。
デコーダビリティ |
グレード |
≧0.62 |
A |
≧0.50 |
B |
≧0.37 |
C |
≧0.25 |
D |
<0.25 |
F [Fail] |
シンボル中のバーやスペースの線幅に太りや細りなどのぶれがあると、デコーダビリティのグレードを下げる原因となります。
|
|
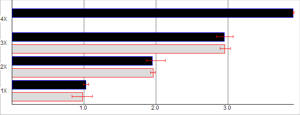 |
|
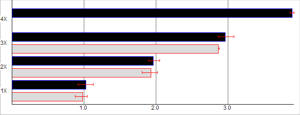 |
|
|
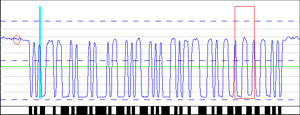 |
|
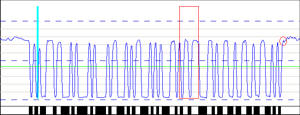 |
|
QC890による検査報告書 |
|
QC890による検査報告書 |
|
検証結果の1つである各バーの太さの平均を求めたグラフを見ると、一番細い隙間(白バー)のぶれが大きくなっている場所があること示しています。
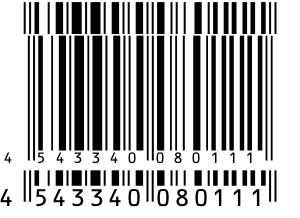
バー幅比較のために、調整(上下方向を圧縮)したバーコードを、センターバー中心で重ねてみました。
どちらの設定も寸法的には標準のバーコードを生成したはずですが、実際に生成されたビットマップの生成寸法が異なっています。
なにも調整しないと、印刷解像度と合っていないため、計算上のまるめ誤差などにより印刷位置が微妙にずれてしまっているようです。
検証機では、直線上の光の反射レベルをもとに数値解析が行われます。
数値報告は非常に重要な要素ではありますが、それだけで全てを判断すると見逃される点もあります。
以下は、テクノベインズ検証サービスで用いる拡大イメージによる評価写真です。
約200倍と顕微鏡レベルまでバーコード印刷像を拡大することで、肉眼では確認できない問題点も、はっきりと確認することができます。
DTPでの版下作成は便利ですが、バーコード生成オブジェクトが生成したビットマップを
、あとから拡大や縮小したりすると、大きく品質が低下します。
また、バーコードフィルムマスターであっても、デジタル的にスキャンや製版されたデータを拡大縮小すると、同様に大きく品質低下を起こす原因となります。
いくつもの条件により、バーコード品質は変化します。実際の印刷やインク・用紙の特性によって光の反射状態やインクのにじみも異なります。
これらは微妙なものが多いので、肉眼での良否判断は非常に難しいと思われます。
印刷工程や流通での汚濁など、あとの工程による品質劣化もありますから、印刷の元となる版下のバーコードは、なるべく高いグレードで作製する必要があります。
そのためバーコードを含んだ流通商品パッケージをDTPで作成する場合、QC890などバーコード検証機で、あらかじめバーコードの品質を検証されることを是非お勧めいたします。